In the region Europe and Central Asia, RWE carries out small to large projects offering professional project management and engineering or consultancy support services tailored to the individual client, ranging from owner’s operators, utilities, industrial clients, lenders, project developers to municipalities.
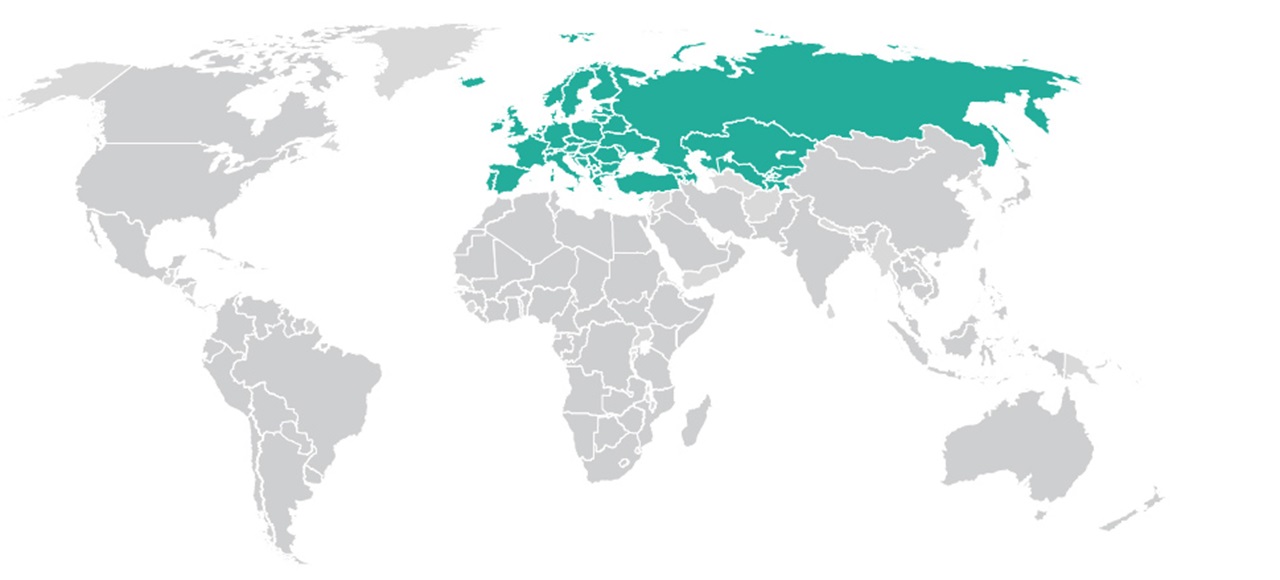
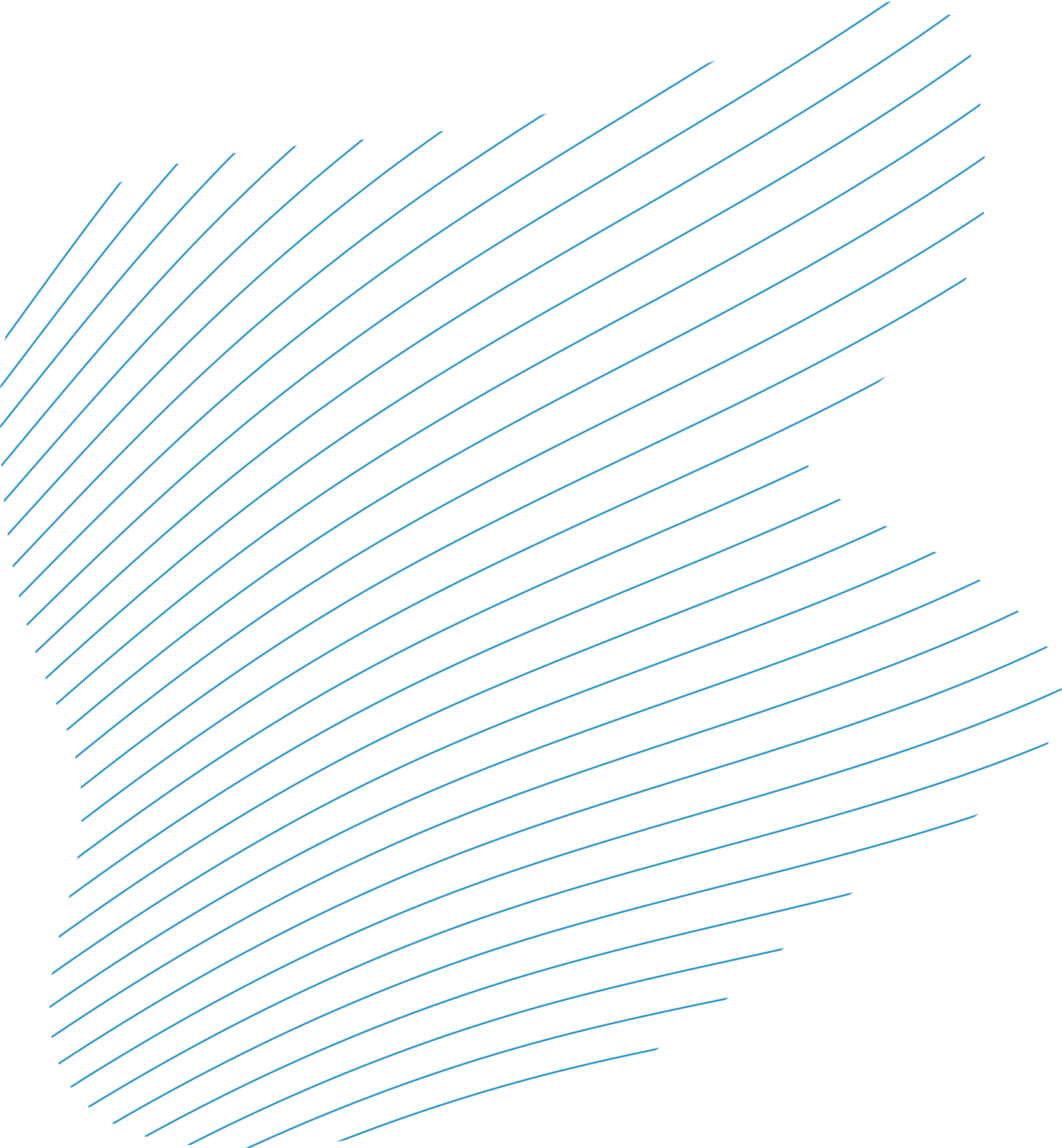
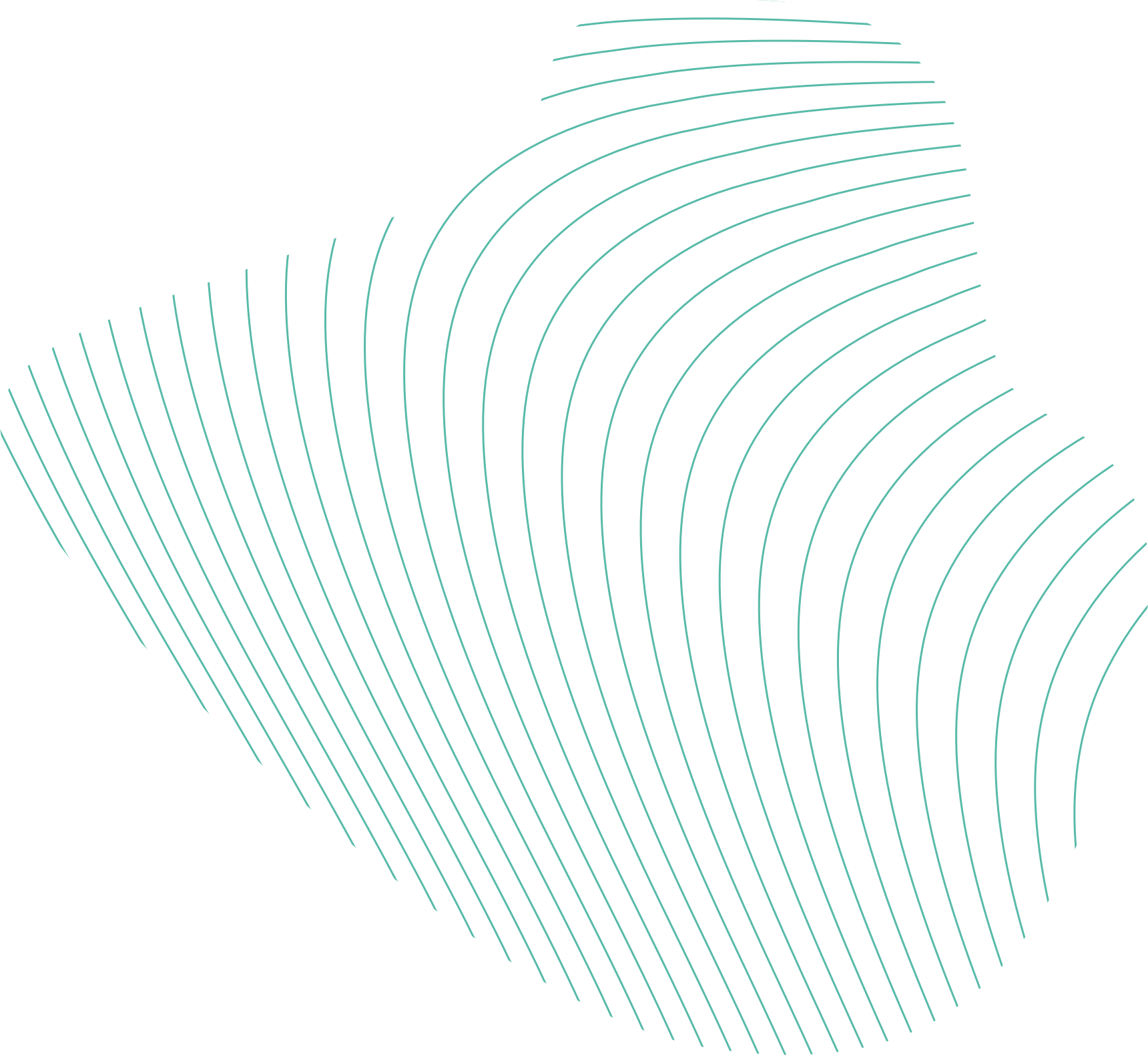
You have any questions, or would you like to find out more about our services?
Please, get in touch with our sales team!
Send e-mailRegardless of the stage throughout the project life cycle, i.e. Feasibility - Procurement - Implementation - O&M - Unbundling and Decommissioning – Demolition, our experts assist and help to transfer knowledge of best practices and standards in energy thermal (gas, waste, coal, biomass), renewables and grid projects.
We provide:
- owners engineering related services
- specialist consultancy services
- lenders engineering services
- quality services and material testing in our own laboratories
- gas turbine maintenance services
- environmental and efficiency improvement projects for existing power plants
Regarding renewable energy technologies, we act as technical advisor especially in onshore and offshore wind, solar thermal, PV, biomass and hydropower. Hydrogen and battery applications are in the focus of our future energy solution projects.
In terms of grid projects, we support grid operators particularly in this region with transmission grid projects and the implementation of line construction works. Furthermore we offer mining services involving exploration, resource and reserve estimation, project assessment and provision of assistance during construction and commissioning at all stages of mine operation, including optimisation, rehabilitation and finally mine closure.
-
Our project references in the region
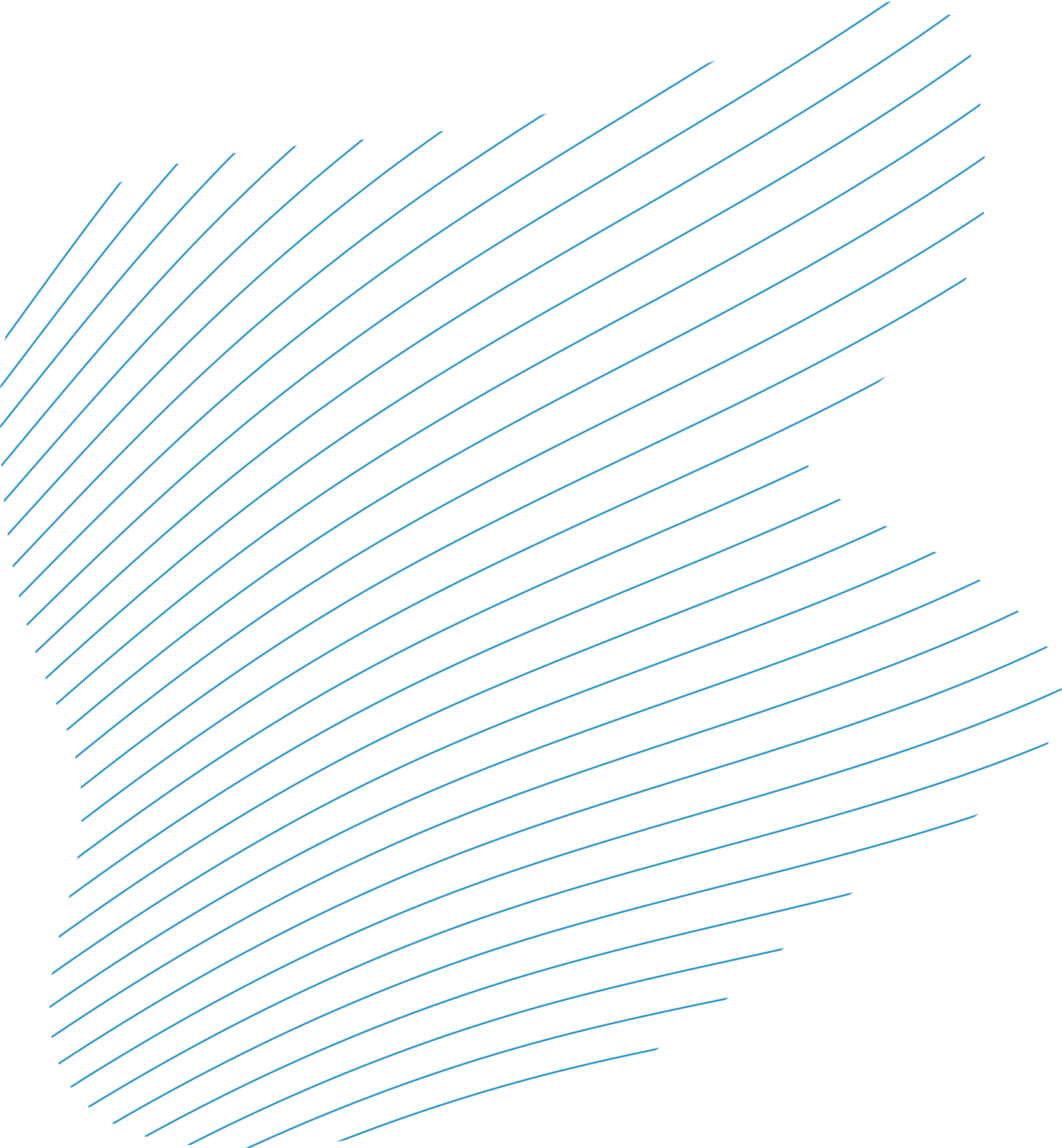
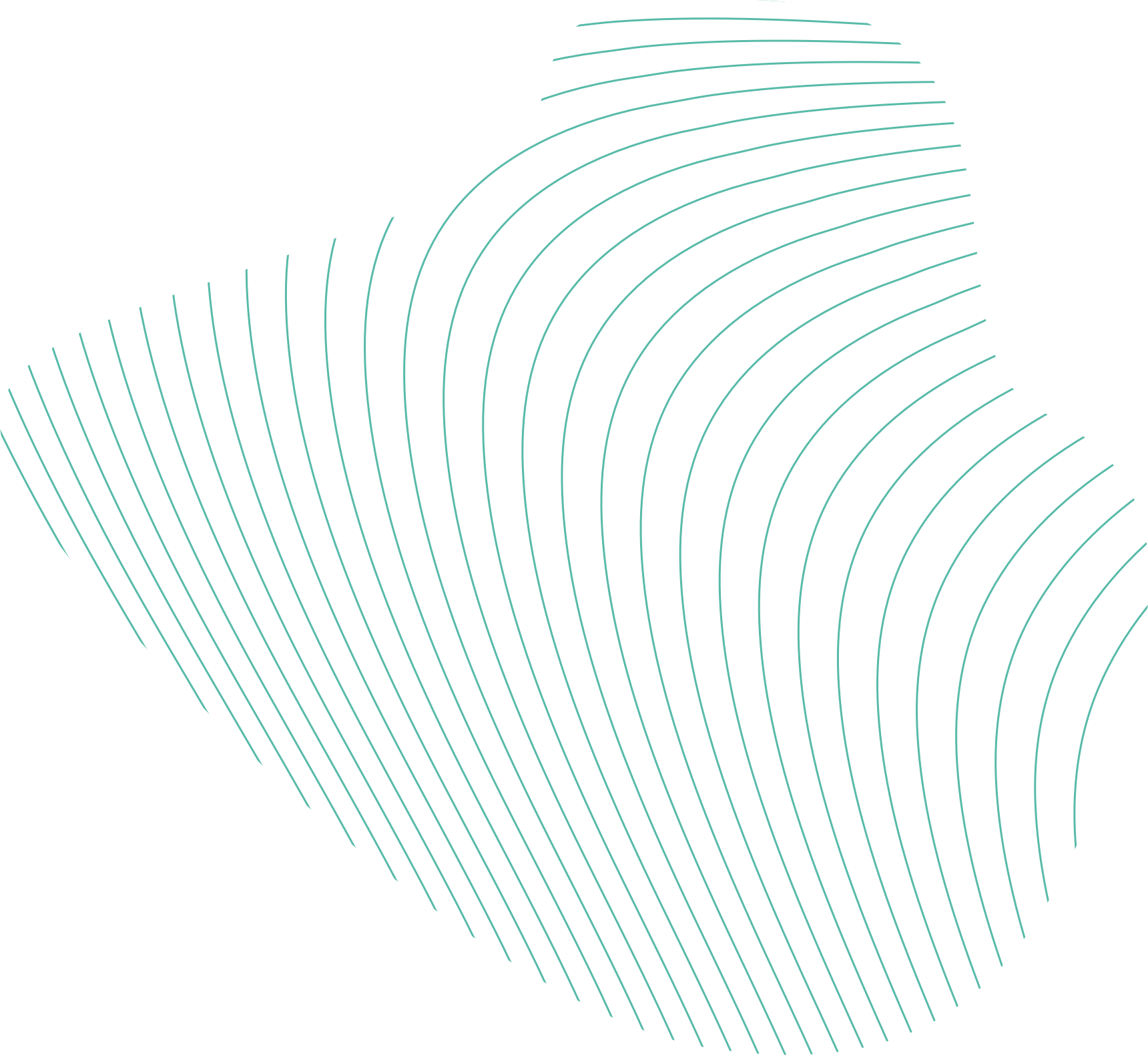